Ryan Yerby
Mechanical Engineer
​Design for Manufacturing: Plastic Injection Molding
Plastic Injection Molding is the process of inserting liquid plastic into a mold to form a particular geometry. It is a common method used to manufacture the majority of plastic parts found in everyday life. There are a few key design principles that should be followed when designing a plastic part that is intended to be molded. These principles are important to ensure the manufactured part resembles the designed part and to ensure the finished product is robust and visually appealing. Failing to adhere to these principles may result in warped dimensions, insufficient structural integrity, and an overall unsatisfactory part.


The first design principle we will cover in this blog post is wall thickness. Wall thickness can be defined as the part thickness at any location. The maximum wall thickness of the part is determined by the specific material used during the injection process. Different materials can be leveraged to display specific material properties that may be advantageous for specific uses. A rule of thumb is no wall should be thicker than 3/8 inch. Wall thickness should also be uniform throughout the part meaning all walls of the part are the same thickness. This is to ensure the part cools uniformly, as differing wall thicknesses may lead to differing cooling rates which could potentially create defects such as warping and sink marks.
The next design principle is to avoid sharp corners and to include radii wherever possible. A sharp corner can be defined as an area where any two walls meet and create a seam such as the interface between the wall and bottom of a box. Sharp corners can be brittle and hinder material flow during the injection process. By including radii, or curved edges, in places that would typically be sharp corners can drastically improve the quality and strength of the part and decrease the chances of part defect.


The third design principle we will discuss is draft angles. The purpose of draft angles is to allow the part to be removed from the mold. Draft angles of approximately 1-5 degrees limit the suction caused by the difference in pressure when the part is removed. Failure to include draft angles could result in part damage and defect upon removal from the mold. If draft angles hinder the part functionality, the mold bust be redesigned to alter the parting line of the mold.
Because wall thickness is limited in plastic injection molding, it is important to include ribs in part designs. Ribs are thinner part geometries that provide structural support to improve the durability of plastic parts. You may have noticed ribs in household plastic items such as the inside of a television remote. Ribs are essential when designing for durability and applications with non-negligible loads.

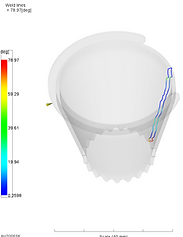
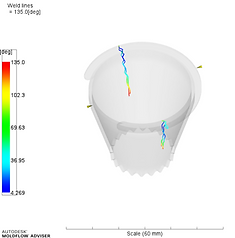
The final design consideration covered in this post is gate locations. Gates are where liquid plastic is injected into the mold. Gates locations may leave small defects on the specific region of the part so gate locations must be strategically positioned to maximize visual appeal of the product. Different gate locations and strategies will also alter the fill and cycle times of the manufacturing operation. This becomes increasingly important with scale. Gate locations also determine how material flows into the mold. Factors such as air bubbles and weld lines should be considered when analyzing gate locations. Mod design software is a useful tool to determine gate locations.